咪唑啉緩蝕劑的合成
近年來,我國陸地油田有相當一部分已進入注水開采的中、后期,油井綜合含水不斷上升,產出水礦化度較高,同時伴有大量侵蝕性物質,受這些綜合因素的影響,在油氣井注水開發中,從油水井地下管柱到地面管道和儲罐及各種工藝設備都會遭到腐蝕,造成巨大的經濟損失,嚴重的還會造成災難性事故和環境污染。 對于含二氧化碳及硫化氫的高礦化度偏酸性的污水,咪唑啉類緩蝕劑具有很好的緩蝕效果。咪唑啉是含有兩個氮原子的五元雜環化合物,除了主體雜環外,還有與雜環上N成鍵的具有不同活性基團支鏈和烷基碳鏈長度不同的疏水支鏈。疏水烷基碳鏈可以在金屬表面附近形成一層有效的疏水層。所形成的疏水層,即可以對電極表面起到一定外圍屏蔽作用,也能阻礙具有腐蝕性能的反應物在腐蝕界面上的遷移。活性基團支鏈可以顯著提高緩蝕劑分子的溶解性,通常還可同金屬表面的孤對電子形成配位鍵而產生化學吸附作用,而達到提高緩蝕性能得的作用。 |
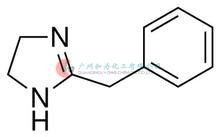 |
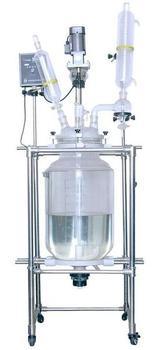 |
常用的合成咪唑啉的方法為:分別取一定量的脂肪酸、多胺和二甲苯放入裝有溫度計、回流冷凝管和分水器的三口燒瓶中,升溫到140-150℃附近進行酰胺化反應,然后升溫到180-250℃反應進行環化反應。反應結束后,即得到淡黃色的咪唑啉產物。根據具體使用環境,還可以用氯化芐、氯乙酸鈉與咪唑啉發生反應,形成咪唑啉季銨鹽。
咪唑啉與及其衍生物類緩蝕劑的合成主要受到生產的水及溫度的影響:
(一)水的影響 在反應過程中酰胺化和環化兩個過程都生成了水,但水的存在對反應的繼續進行存在阻礙作用。原因主要是以下兩點:第一,從化學動力學角度,酰胺化和環化反應所生成的水阻礙了正方向反應的進行,使整個合成反應減速;第二,在水存在的情況下,生成產物極其容易水解以及發生其他的副反應,使得產物的純度降低。在這種清況下,對所合成咪唑啉中間體應盡快進行除水操作。通用的去除水方法有兩種(1)真空法或氮氣保護:進行第一次脫水,先對反應體系抽真空或通入氮氣,使得反應物在非常低的壓強下或氮氣保護下充分地混合并進行加熱處理,之后采用程序升溫與逐漸降低壓力或減少氮氣的方法,除去體系中的水分,進行第二次脫水。(2)溶劑法:其中第一次脫水是在常壓下進行的,是以甲苯或二甲苯做攜水劑與水共沸,然后將水從容器中帶出,以此推動反應的繼續進行。再在減壓的條件下進行升溫,進行第二次脫水環化。其終點可以用反應生成的水和產物的酸度值來判斷。這兩種方法各有利弊:溶劑法的合成產物,反應溫度很低,并且生成的產物不易變質變色,但反應終點的判斷需要的時間較長,收率也比較低;而真空法存在的問題則是對整個反應過程所用儀器的密封性要求較高,否則生成物容易變質,原料中胺也較易被抽走,氮氣法不僅氮氣消耗量大,而且也容易將反應原料中的胺帶走。也可以根據上述兩種方法的特點,將其優缺點進行整合,前期溶劑法,后期真空或氮氣保護法的混合法。目前,工業生產中大多數采用甲苯和真空脫水的方法。甲苯脫水法優點是出水比較平穩,多胺不易被抽出,但回收甲苯較為麻煩。真空脫水法的優點是,較簡單,但多胺易被抽出,使生產物質中所含有的二酰胺過多。二酰胺為反應的副產物,一般情況下不能轉化為咪唑啉類物質。并且不能進行季銨化反應,是合成咪唑啉產物中的主要雜質。生成物中二酰胺的百分含量被作為評定咪唑啉優劣的標志。二酰胺的含量過高,產物季銨化后極容易沉淀,最終產物的穩定性下降。 |
(二)反應溫度的影響 反應溫度是制備咪唑啉緩蝕劑反應中的重要因素。咪唑啉中間體的合成過程是經過兩步脫水。國內對咪唑啉環化過程的反應溫度段的溫度高低進行了很深入地研究,但并沒有達成一致認識。有研究認為在酰胺化脫水段,溫度在140-160℃,反應時間在1-1.5h較為合適。在環化脫水階段,溫度應在180-250℃,最高的反應溫度不應超過270℃,反應的時間應在1.5-2h較為理想。而也有研究指出環化脫水反應的溫度,一般應在240-250℃,反應時間在8-16h不等。還有研究說明在含有攜水劑的情況下,150℃也并不是最佳的反應溫度,逐步升溫的方法更合理和更有優勢。 屈人偉等將環烷酸和二乙烯三胺按1:1.2的摩爾比混合,在100-120℃下預反應0.5小時,然后升溫至180℃反應1小時,再升溫至210℃反應1小時,得到咪唑啉。將合成的咪唑啉分別與環氧乙烷和氯化芐按摩爾比1:7和1:1在一定條件下反應,得到深褐色環烷酸咪唑啉的乙氧基化產物和季銨化產物,在200 mg/LH2S-3%NaCl-H2O污水體系中評價了制備產物的緩蝕性能。對于乙氧基化產物,隨著濃度的增加其緩蝕率增大,但在濃度達到80mg/L后緩蝕率增加很慢。對于季銨化產物,隨著濃度的增加其緩蝕率也不斷增大,在濃度100mg/L時緩蝕率約可達90%。在相同濃度下,季銨化產物的緩蝕率比乙氧基化產物的高。這可能與環烷酸咪唑啉分子中引進了芐基,加強了緩蝕劑對金屬表面的吸附有關。 李文靜等將二乙烯三胺和羧酸按摩爾比1:(1.05-1.2)加入帶溫度計、回流冷凝器、攪拌器、分水器的四口燒瓶,取25-40mL甲苯(或二甲苯)作攜水劑。緩慢升溫至回流,保持此溫度,反應2-2.5 h,隨后緩慢升溫至220-230℃,反應一定時間。蒸出未反應的二乙烯三胺和攜水劑,冷卻,即制得咪唑啉產物。由于咪唑啉不溶于水,為了提高咪唑啉在油田污水中的溶解性,進一步增強其緩蝕效果,對其進行水溶性改性實驗。將咪唑啉產物加入三口燒瓶中,加熱到一定溫度,加入三氯化磷、甲醛等改性劑,反應一定時間,冷卻,即得水溶性咪唑啉衍生物緩蝕劑。制備的水溶性咪唑啉衍生物緩蝕劑為有機吸附膜型緩蝕劑,為了增強其在高溫、高氯離子含量、高礦化度污水中的緩蝕效果,選擇磷鹽、硫脲等作為緩蝕增效劑,確定了復合緩蝕劑配方:20%-30%主體緩蝕劑、40%-50%磷鹽、10%-15%硫脲及20%-30%其他配料。通過實驗證實,得到的復配型緩蝕劑的緩蝕率和穩定性高于油田常用緩蝕劑;添加量為10~20mg/L時,即可達到滿意的緩蝕效果。對緩蝕劑作用機理研究證實,咪唑啉衍生物為吸附膜型緩蝕劑,緩蝕劑分子由電負性較大的O、N、P等原子為中心的極性基與C、H原子組成的非極性烷基組成。這些性能不同的基團在金屬的表面起不同的作用,主要通過物理或化學吸附吸附到金屬表面,形成吸附保護膜。緩蝕劑分子中具有未成鍵電子對的元素可進入金屬結構的空軌道形成配位體,從而產生緩蝕劑分子的吸附層,抑制金屬的腐蝕。 史足華等將松香、蓖麻油、二乙烯三胺、二甲苯按一定比例加入到不銹鋼反應釜中,密閉,通冷卻水,升溫至120℃,恒溫0.5 h,攪拌,升溫至160℃,反應2 h,隨著反應的進行,生成部分低分子反應產物,用二甲苯作為攜帶劑將其逐漸蒸出,進入接收器,通過控制冷卻水的流量來控制接收器中二甲苯的蒸出速度并計量,再升溫至210℃,反應6 h,待二甲苯全部蒸出,即表明已生成咪唑啉化合物,降溫至90℃,加入一定量的添加劑和水,使合成的中間體質量分數為62%,最后將得到的產物與水按質量比1:6復配,即得到最終的污水緩蝕劑。該樣品的外觀為棕紅色粘稠液體,pH為8~9,固體相質量分數≥8%,樣品易溶于水,無沉淀及分層現象。由于松香型咪唑啉和蓖麻油型咪唑啉化學結構和相對分子質量各異。兩者相互補充,能夠在金屬表面形成致密的保護膜。分子結構中的極性基團吸附在金屬表面上,而長尾巴非極性基團由金屬表面向溶劑排列。一方面由于緩蝕劑改變了金屬表面的電荷狀態,增大了腐蝕反應的活化能,使腐蝕難以進行;另一方面非極性基團多數排列在金屬表面,形成疏水膜,阻止了與腐蝕反應有關的電荷或物質移動,達到抑制腐蝕的目的。該污水緩蝕劑的優點在于:由松香與二乙烯三胺所合成的松香型咪唑啉在金屬表面吸附性好,空間位阻大,形成的吸附膜有縫隙;而蓖麻油與二乙烯三胺所合成的蓖麻油型咪唑啉因相對分子質量小、空間位阻小,能夠較好地填補松香型咪唑啉所形成的吸附膜縫隙,兩者相互彌補,使得緩蝕劑在金屬表面形成比一般咪唑啉型緩蝕劑更加致密的保護膜,抑制了腐蝕的進行。 黃光團等使用長鏈脂肪酸、多胺、甲醛和三氯化磷等為原料合成了咪唑啉有機膦酸類緩蝕劑。在模擬油田注水條件下,對緩蝕劑性能進行了評價,評價結果表明當投加量達到50mg/L時,緩蝕率可達90%。
本文版權為荊門鑄鼎新材料有限公司(www.china-njtz.com)所有,轉載請注明出處。
2013年7月12日
本站關鍵詞: 酸化緩蝕劑 | 酸洗緩蝕劑 | 二氧化碳緩蝕劑 | 潤濕抑塵劑 | 緩蝕阻垢劑 | 污水緩蝕劑 | 硫化氫緩蝕劑
|